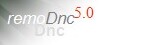 |
|
Topic: Drip Feeding a BOSS 8
|
By: Zack | Posted on: Jun 29 2008 at 01:48:59 AM | Does anyone know whether the trial version of Easy DNC will drip feed to a Bridgeport BOSS 8? Furthermore, has anyone accomplished this with the official version or even any other DNC package?
I would really appreciate some enlightenment on this. | |
By: Matt | Posted on: Jun 29 2008 at 09:45:37 AM | The question ought to be whether a Boss 8 is capable of drip feeding.
If the Boss 9 is capable of drip feeding then it should be able to drip feed with the trial version of easyDnc. | |
By: Zack | Posted on: Jun 29 2008 at 05:04:21 PM | Matt
From my understanding the BOSS 8 can be drip fed. There are 3 input protocols in the menu.
1.) PTR (Paper Tape Read)
2.) DNC
3. REM (Remote)
We use the Remote function to load programs. I think that the DNC function allows drip feed. However, I can`t seem to find any setting on the EasyDNC for this. | |
By: Guest | Posted on: Jun 30 2008 at 11:39:39 AM | easyDnc doesn`t need any specific setting. It`s controlled by `Flow Control`.
As long as easyDnc has flow control enabled (Hardware RTS/CTS or Software XonXoff) then the flow of data (the drip feeding) will be controlled by the CNC.
On something like a fanuc you set the CNC into `Tape or DNC` mode and hit cycle start. At this point the CNC doesn`t do anything. Then go to the computer and hit SEND. As soon as data begins to flow the CNC starts cutting and the flow of data is managed by the CNC using flow control.
If the CNC cuts for a minute and then throws an overflow alarm then you don`t have flow control enabled correctly.
I mentioned the procedure for a fanuc because I don`t actually have a Boss but I imagine the basicl principle is the same. | |
By: netpipe | Posted on: Dec 28 2008 at 02:38:05 PM | I have a Bridgeport Boss 6 and do have it drip feeding. Not a simple task because it took me 1 year to investigate and get it working.
REGARDLESS of the type of software used.
The boss controllers are for the most part very dump. No handshaking therefore not able to tell the pc to wait or when to give it more data. Additionally, most of the Boss controllers only have 8K. That`s only 8,000 characters. Maybe 400 lines of code.
Currently, I do mostly 3D solids and the code generated has ranged from 9,000 lines to over 325,0000 lines of code. Never fails.
You MUST utilize a BTR (Behind Tape Reader) board. Some come with 8-32MB of storage. However, you don`t need to have the larger model. PC connects to one side of the BTR, the other connects to the Boss controller using the TAPE interface.
You need to inject some characters in your GCODE to tell the controller to run up to a certain point and when reached, it will dump existing memory and load the next block of code (size is adjustable).
Once it was working, it became a pain to manually ingest the commands into the code so I wrote a simple program to automatically do it for me. Takes about 3 seconds for 10,000 lines of code
I have given the program and detailed information (NO CHARGE) to anyone that needs it. | |
By: Support | Posted on: Dec 29 2008 at 12:43:57 PM | The previous post from Netpipe (Rick) has been edited by the forum admin.
Netpipe (Rick) suggests that at least his Boss was not capable of drip feeding and in my experience that`s the case with quite a lot of old CNC. In those cases an additional device can be fitted (a BTR)
Rick goes on to say that he has some expertise and knowledge on the subject of BTR and drip feeding Boss CNC which he`s happy to give free of charge so please contact him at.
rick at telcoautomation dot com | |
Reply - add a comment to this topic.
You may enter letters, numbers and standard punctuation only. HTML and other scripts/tags will be rejected.
|
|
|