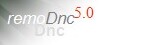 |
|
Topic: Error 17 Parity Error
|
By: Bare Knuckle | Posted on: Apr 18 2008 at 03:29:39 PM | I can`t get my machine to receive code, I keep receiving and E-17 Parity Error. The machine is a Mitsubishi Meldas. and the E-17 Code error definition
is:
"Although CNC Transmits DC3 to Host, it recieves data of 10 bytes or more from the Host, thus terminates communication."
Thoughts? | |
By: Support | Posted on: Apr 18 2008 at 05:21:45 PM | The exact meaning of that message is that whenever the CNC sends a Stop (Xoff) command to the computer the computer doesn`t stop quick enough.
You can do one or more of the following.
1) Disable the Windows FIFO (see below)
2) Make sure XonXoff is enabled in easyDnc
3) Lower the BaudRate
4) Increase the BlockDelay in easyDnc setup
The Windows FIFO is a com port setting which you get to via the Windows Control Panel>System>Hardware>Device Manager>Ports(Com&Lpt)
Select the com port>PortSettings>Advanced
this displays a window with sliders to adjsut FIFO. Slide these down to zero and then unchceck the box to disable FIFO. | |
By: Bare Knuckle | Posted on: Apr 18 2008 at 08:03:02 PM | Thanks for the response, now I`m getting an E08 Error message but all my parameters on the CNC are the same as the COM port and the settings in the software. I have been able to receive from the CNC but unable to send to the machine. | |
By: Bare Knuckle | Posted on: Apr 18 2008 at 09:04:19 PM | Ok back to the E17 Error
1)I`ve disable the Windows FIFO setting
2)I`ve enabled RTS/CTS mode instead of Xon/Xoff because our machine doesn`t send the the go ahead to easyDNC. and I have the CNC set to RTS/CTS as well.
3)BaudRate is set at 1200
4)BlockDelay is at 200
Still Getting E17 Parity H Error
Suggestions?
[quote:5d5583790a="support"]The exact meaning of that message is that whenever the CNC sends a Stop (Xoff) command to the computer the computer doesn`t stop quick enough.
You can do one or more of the following.
1) Disable the Windows FIFO (see below)
2) Make sure XonXoff is enabled in easyDnc
3) Lower the BaudRate
4) Increase the BlockDelay in easyDnc setup
The Windows FIFO is a com port setting which you get to via the Windows Control Panel>System>Hardware>Device Manager>Ports(Com&Lpt)
Select the com port>PortSettings>Advanced
this displays a window with sliders to adjsut FIFO. Slide these down to zero and then unchceck the box to disable FIFO.[/quote:5d5583790a] | |
By: Support | Posted on: Apr 19 2008 at 12:02:57 PM | In order for RTS/CTS to function you must have pins 4 and 5 of the CNC connected to the computer.
When using XonXoff it`s common to just make a short connection between those two pins at the CNC end of the cable but that won`t work for RTS/CTS flow control.
If your computer has a 9pin connector then it`s:-
PC Pin 2 to CNC Pin 2
PC Pin 3 to CNC Pin 3
PC Pin 5 to CNC Pin 7
PC Pin 7 to CNC Pin 5
PC Pin 8 to CNC Pin 4
Then at the CNC short pins 6,8 and 20 together.
That cable will work for RTS/CTS flow control and also for XonXoff so I usually recommend making up a cable like that and it`ll work for both types of flow control.
In your first post you mentioned an error something like this:-
[quote:48a5ea3083]Although CNC Transmits DC3 to Host, it recieves data of 10 bytes or more from the Host, thus terminates communication[/quote:48a5ea3083]
Does the error still mention DC3 ? Previously you mentioned Error 17. Now you`re saying it`s 17H is that the same ?
The Meldas control can be strange in that they often need to be set to 8Bits Even Parity while the PC is set to 7Bits, Even Parity.
Sounds strange setting the CNC to 8 bits while the PC is set to 7 but that`s because the CNC counts the parity bit (7 databits + 1 parity bit = 8 ) Whereas a PC doesn`t count the parity.
So, try the CNC at 8Bits, Even Parity, 2 Stop Bits. And set easyDnc to 7Bits, Even Parity, 2 Stop Bits.
Also check in the CNC setting for `other` parity settings. Some have a `Block Parity` check which can be disabled. Basically in the parity setting set it to Even but wherever it says enabled parity check set that to Off.
There`s lots of `try this or that` in this post. Sorry. When you reply please let me know which meldas control (model number) it is and I can maybe be more precise. | |
By: uli kolb | Posted on: Aug 21 2008 at 01:27:28 PM | [quote="Bare Knuckle"]I can`t get my machine to receive code, I keep receiving and E-17 Parity Error. The machine is a Mitsubishi Meldas. and the E-17 Code error definition
is:
I have the same problem. have you got this problem? please help me | |
By: uli kolb | Posted on: Aug 21 2008 at 01:36:50 PM | i have a meldas m320. i use 4800 / 8/2/E . it is easy and without problems to recive datas from the machine to the pc. but when i start sending to the machine , i become the e17 parity h - error. most of the time, the first line is into the machine and then the error goes to display. i have no idea....-(( | |
By: Support | Posted on: Aug 21 2008 at 04:52:22 PM | Have you tried all the suggested solutions ? | |
By: Dave6 | Posted on: Nov 15 2008 at 07:25:27 PM | Was this ever solved? If so how I have the same problem with my Meldas L3. | |
By: Guest | Posted on: Nov 16 2008 at 03:36:32 PM | If the error getting is this:-
[quote:de2ae34c07]Although CNC Transmits DC3 to Host, it recieves data of 10 bytes or more from the Host, thus terminates communication."[/quote:de2ae34c07]
Then the problem is flow control.
The mention of DC3 indicates that you`re using XonXoff flow control - try all the things mentioned above such as - switch off the windows FIFO - Increase the Block Delay in easyDnc setup - Use a lower baud rate.
If you can you should switch to RTS/CTS flow control but you`ll need to make sure your cable is has the correct pins connected. RTS/CTS will not work unless your cable us like this:-
PC Pin 2 to CNC Pin 2
PC Pin 3 to CNC Pin 3
PC Pin 5 to CNC Pin 7
PC Pin 7 to CNC Pin 5
PC Pin 8 to CNC Pin 4
Then at the CNC short pins 6,8 and 20 together.
If you`re stuck to using XonXoff and you`re using a USB adapter then the flow control problem is caused because the USB buffers are very big and once data is in the buffer (up to 128 bytes) then flow control has no control over those bytes. Remember the error description mentioned 10 bytes. That means that at that moment the CNC had 10 free byte spaces but the USB sent up to 128 bytes which obviously doesn`t fit causing an overflow error. | |
By: bladde | Posted on: Feb 14 2015 at 12:08:32 PM | I had this problem today witch is about 7 years later lol all i did to resolve this issue was to move my delay up from 50 to 60 but thanks for the topic helped me to confirm what i already had. these things can be such a pain sometimes > | |
By: RAUL | Posted on: Dec 11 2017 at 06:04:07 PM | HOLA TENGO UN PROBLEMA CON UN MELDAS 500 ME MARCA PARITY ERROR SR=0000 ERROR AT OR NEAR $50043382 ME PODRIAN AYUDAR PORFAVOR?
| |
By: Guest | Posted on: Dec 13 2017 at 02:05:54 PM | IO Parameters
4 (Parity Enabl) 0 = No
5 (Parity) = Even
6 Databits 3 = 8 Bits
Thing to notice is that Parameter #4 is parity. Make sure this is Not Enabled
Also Parameter #6 is "8" (8Bits) So the CNC is 8bits but still set the DNC software is 7bits Even. | |
By: raul | Posted on: Feb 7 2018 at 06:49:45 PM | alguien tendra los parametros que los pueda compartir es una viper mill v-850 control mitsubishi meldas 500
| |
By: Guest | Posted on: Mar 13 2018 at 02:09:47 AM |
i have maybe same problem. Can anyone help me?
Parity Error
SR=0000
Error at or near $5004337A
PC=5004337A SP=0000BFD0 | |
By: Guest | Posted on: Mar 13 2018 at 01:18:39 PM | Its likely a receive buffer overflow in the cnc. To much data too fast.
What settings do you have in the dnc software?
Check that flow control is xonxoff.
Try a lower baud date (changing in the cnc as well as in the dnc computer)
In the dnc software setup increase the block delay. | |
By: J.W. | Posted on: Aug 8 2019 at 01:40:40 AM | Who ever you are that said do 8 bits at cnc and 7 bits at pc
Thank You very much for thinking outside the box.
Solved my problem
J.W. | |
By: Guest | Posted on: Sep 7 2022 at 04:49:37 PM | IF anyone have this error:
Parity Error
SR=0000
Error at or near $5004337A
PC=5004337A SP=0000BFD0
i have a possible error solve at sags_v@hotmail.com | |
By: Guest | Posted on: Sep 9 2022 at 04:57:52 AM | This error message on the CNC console
[i][B]"Although CNC Transmits DC3 to Host, it recieves data of 10 bytes or more from the Host, thus terminates communication."/B][/i]
that always relates to a buffer overflow in the CNC's receive buffer that is usually caused by Flow Control not working efficiently.
#1 Make sure flow control is enabled in the DNC software
#2 Make sure that FIFO buffers are disabled in Windows Device Manager. Go into Windows Device Manager and you see a list of all the devices in the computer, memory, disks, processor etc. But also "PORTS COM & LPT". Open that section to see a list of the COM ports in the computer. Identify the com port you're using. Open that one and go to "Advanced" in there you should see sliders for FIFO. Slide them right down to zero and there's also a checkbox to disabled.
Once you've disabled FIFO I don't know if the computer needs reboot. Some devices need it others don't. Maybe reboot anyway and go back into device manager to see if the FIFO is still disabled.
Now try sending to the CNC again. Does the problem still happen? If it does go into the DNC setup and increase the TX Block Delay (bigger delay)
| |
Reply - add a comment to this topic.
You may enter letters, numbers and standard punctuation only. HTML and other scripts/tags will be rejected.
|
|
|